BAUWEISEN
Verbundbürsten
Die Bürsten aus Ceramix® Schleifnylon wurden für den Einsatz mit Werkzeugen, in Roboterzellen und CNC-Maschinen entwickelt, um Verschwendung und Nicht-Standardisierung von manuellen Entgratungsvorgängen zu vermeiden.
SIT’s exklusiver Zugang auf die Produktpalette von Ceramix®, mit einem starken Fokus auf abrasive Spezialborsten, erweitert das Angebot an industriellen Bürsten für unsere Kunden.
Materialien
Diese Bürsten aus abrasivem Nylon bestehen aus CeramiX®-Borsten, die in einen Urethanverbundstoff eingeschmolzen sind.
CeramiX® ermöglicht eine 3 bis 5 Mal schnellere Schneidwirkung als herkömmliche abrasive Borsten. Das abrasive Mineral wird in kleineren Partikeln verbraucht, so dass der größte Teil des Minerals an der die Oberfläche bearbeitenden Borste haften bleibt.
3 Hauptmerkmale tragen zu der hohen Leistung dieser Borsten bei:
- Bruchbeständigkeit
- Härte
- Selbstschärfend
Diese Eigenschaften führen zu einer erhöhten Leistung der Bürsten aus abrasivem Nylon CeramiX®, die mit dem keramischen Schleifkorn 321 mit Eigenschaft 3M™,(erhältlich in den Körnungen 220, 180, 120, 80 und 46) das in die Borsten eingearbeitet ist, hergestellt werden.
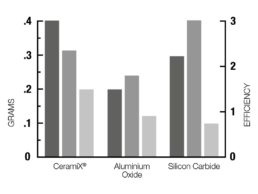
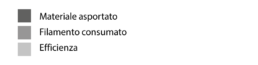
Test 1: Aluminiumplatte 1750 U/min
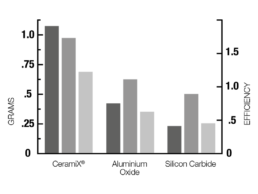
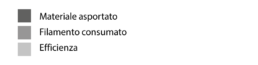
Test 2: Kaltgewalztes Stahlblech 1750 U/min.
Korn und Borstendurchmesser
Grana | Diametro filamento / Filament diameter | ||
---|---|---|---|
Grit | mm | inch | |
46 | 1,65 x 2 | 0,065" x 0,080" | * sezione ovale / oval shape |
1,7 x 2,3 | 0,068" x 0,090" | ||
80 | 1 | 0,040" | |
1.4 | 0,055" | ||
1,1 x 2,3 | 0,045" x 0,090" | * sezione rettangolare / rectangualr shape | |
120 | 0.7 | 0,028" | |
1 | 0,040" | ||
180 | 0.9 | 0,035" | |
220 | 0.6 | 0,22" |
Die für CNC-Maschinen gelieferten Standardfilter (Papier, Gewebe, Viskose, Filz) sind so ausgelegt, dass sie Partikel bis zu 5 Mikron – 0,0002″ – filtern. Bitte fragen Sie Ihren Lieferanten nach dem am besten geeigneten Filter.
Umrechnung Korn - Mikron - Zoll
Grana / Grit Size | Micron (valore medio / average) | Inch (valore medio / average) |
---|---|---|
46 | 356 | 0.014 |
60 | 254 | 0.010 |
80 | 165 | 0.0065 |
100 | 122 | 0.0048 |
120 | 102 | 0.0040 |
180 | 76 | 0.0030 |
220 | 63 | 0.0025 |
240 | 50 | 0.0020 |
320 | 31 | 0.00122 |
500 | 19 | 0.00075 |
800 | 12 | 0.00047 |
1000 | 7 | 0.00028 |
Jedes Schleifkorn hat eine andere Größe. In der Tabelle ist ein Durchschnittswert angegeben.
Betriebsparameter
Anfangsdrehzahl und Scheibenbürsten Motorgröße
D | Dry RPM | Motor | |
---|---|---|---|
mm | inch | ||
50 | 2 | 1750 - 2500 | 1/4 HP |
76 | 3 | 1750 - 2500 | 1/4 HP |
102 | 4 | 1750 - 2500 | 1/4 HP |
127 | 5 | 1500 - 1750 | 1/4 HP |
152 | 6 | 1250 - 1750 | 1/2 HP |
203 | 8 | 800 - 1200 | 3/4 HP |
254 | 10 | 700 - 800 | 1 HP |
305 | 12 | 600 - 700 | 1 HP |
355 | 14 | 500 - 600 | 1 HP |
Anfangsdrehzahl und Motorgröße für Rund- und Scheibenbürsten
D | Dry RPM | Motor | |
---|---|---|---|
mm | inch | ||
50 | 2 | 1750 - 2500 | 1/4 HP |
76 | 3 | 1750 - 2500 | 1/4 HP |
102 | 4 | 1750 - 2500 | 1/4 HP |
127 | 5 | 1500 - 1750 | 1/4 HP |
152 | 6 | 1250 - 1750 | 1/2 HP |
203 | 8 | 800 - 1200 | 3/4 HP |
254 | 10 | 700 - 800 | 1 HP |
305 | 12 | 600 - 700 | 1 HP |
355 | 14 | 500 - 600 | 1 HP |
LEGENDE
D = Scheiben- oder Kreisdurchmesser
Dry RPM = Empfohlene Anfangsdrehzahl für trockene Anwendungen
Motor = Empfohlene Motorgröße in PS (unter Berücksichtigung eines Bürstenbereichs von 25 mm – 1″)
* Bei Anwendungen mit Kühlmittel können bis zu 40 % höhere Drehzahlen innerhalb der für die Bürste und das Werkzeug zulässigen Höchstdrehzahl erreicht werden.
Vorschubgeschwindigkeit auf unterschiedlichen Materialien
Velocità Avanzamento / Feed Rate | ||
---|---|---|
mm/min | inch/min | |
Acciaio Inox - Leghe d'acciaio / Stainless Steel - Alloy Steel | 300→450 | 12→18 |
Acciaio dolce - Ghisa / Mild Steel - Cast Iron | 630→760 | 25→30 |
Alluminio - Non ferrosi / Aluminium - Non ferrous | 890→1270 | 35→50 |
Scheibenbürsten in abrasivem Nylon arbeiten besser mit Geschwindigkeiten, die ein gutes Eindringen der Borsten auf das Werkstück erlauben.
Höhere Drehzahlen funktionieren nicht so gut wie mittlere Drehzahlen, zumal der auf der Bürste angegebene Wert MAX RPM nicht die optimale Verarbeitungsgeschwindigkeit angibt. Eine gute Faustregel ist die Einhaltung einer Tangentialgeschwindigkeit von weniger als 13 m/s – 2500 ft/min bei Trockenanwendungen und weniger als 18 m/s – 3500 ft/min mit Kühlmittel.
Das Kühlmittel wird immer dann empfohlen, wenn hohe Drehzahlen, hohe Eindringtiefen oder dünne Stärken bearbeitet werden.
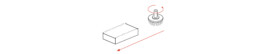
Drehrichtung
Zu Beginn des Bürstvorgangs muss die Drehung entgegengesetzt zur Richtung des Schneidwerkzeugs erfolgen, das den Grat verursacht hat (gleiche Drehung, entgegengesetzte Richtung)..
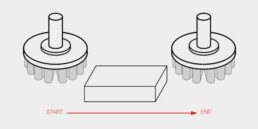
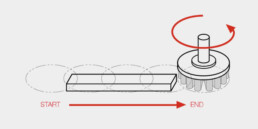
Bürstenbahn
Der ideale Durchlauf der Bürste ist derjenige in die entgegengesetzte Richtung des Schneidwerkzeugs, das den Grat verursacht hat.
Außerdem muss die Bürstenbahn breiter sein als die des Schneidwerkzeugs, damit der Austrittspunkt der Bürste mit dem Ende des Werkstücks zusammenfällt.
Die Bürste beginnt sich zu drehen, bevor sie das Werkstück berührt, und hört auf, sich zu drehen, nachdem sie das Werkstück verlassen hat.
ZEICHNUNG1
Die Drehachse der Bürste muss gegenüber der Längsachse des Werkstücks versetzt sein, um den Kontakt der Borstenanzahl mit dem Werkstück zu maximieren, insbesondere wenn das Werkstück größer als die Bürste ist.
ZEICHNUNG2
Nach Beendigung der ersten Bahn ist es ratsam, die Drehrichtung umzukehren und eine der ersten Bahn entgegengesetzte Bahn einzurichten, um alle Grate zu entfernen.
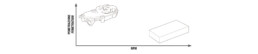
Penetration (Berührungspunkt)
Die optimale Schleifwirkung wird erreicht, wenn die Borstenspitzen über die Oberfläche oder Kante der zu bearbeitenden Komponente gleiten.
Das richtige Gleichgewicht zwischen Drehzahl (RPM), Interferenz/Penetration, Verweilzeit und Schleifkorngröße maximiert die Lebensdauer der Bürste und die Schneidleistung. Die empfohlene Penetration/Interferenz für Rund- und Scheibenbürsten in abrasivem Nylon reicht von 1,3 mm – 0,05″ bis 2,5 mm – 0,100″. Dadurch werden die Lebensdauer der Bürste und ihre Aggressivität maximiert.
FRAME
Regulierung des Borstenverbrauchs
Wie im Abschnitt „Auswahl der richtigen Bürste“ erwähnt, ist es bei CNC-Maschinen möglich, die Belastung der Motoren zu überwachen, um die Werkzeugposition so anzupassen, dass eine konstante Überlagerung oder ein konstanter Druck für eine bessere Bearbeitungsleistung und einen geringeren Borstenverbrauch beibehalten wird. Es gibt 4 gängige Methoden zur Regulierung des Borstenverbrauchs in diesen Maschinen.
Automatische Indexierung: Programmierung einer Regulierung (Indexierung des Werkzeugs auf der Z-Achse) nach einer bestimmten Anzahl von produzierten Teilen
Inspektion: Bearbeitungszentren können die Bürstenoberfläche abtasten, um den richtigen Abstand zwischen den Borstenspitzen und dem Werkstück einzustellen.
Überwachung des Stroms: Durch Ablesen des Nennstroms mit einem Amperemeter ist es möglich, den Werkzeugdruck einzustellen
Manuelle Indexierung: Wenn andere Methoden nicht anwendbar sind, kann der Bediener eingreifen, um die Interferenz auf der Grundlage statistischer Kontrollmethoden oder visueller Inspektion der bearbeiteten Teile manuell einzustellen.
Die Vorteile des Entgratens in Bearbeitungszentren
- Prozessverbesserung:
- Beseitigung des manuellen Entgratens und der weiteren Bearbeitung von Teilen außerhalb des automatischen Zyklus
- Vereinfachung des Arbeitszyklus (Zeit und Kosten)
- Geringerer Zeit- und Kostenaufwand für Transport und Logistik/li>
- Höchste Präzision bei der Entgratung jedes Werkstücks
- Homogenität beim Entgraten von Werkstücken
- Perfekte Wiederholgenauigkeit und Standardisierung des Vorgangs
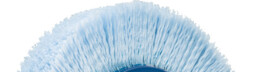