INDUSTRIAL APPLICATIONS
Brushes for the pipeline industry
In the Pipeline industry, from pipes’ manufacturing to their posing on the ground or offshore, the brushing treatment holds a very relevant aspect of each working cycle. SIT offers a wide range of very high quality brushes tested and appreciated worldwide.
Chamfer preparation and weld cleaning
Weld seams preparation and cleaning are very important in the pipeline posing process. The typical hard working environment requires maximum performance of the used tools.
The choice of the brush as a weld cleaning tool affects a higher efficiency (complete welding debris removal on every single layer) a longer service life and the resulting savings during the brush replacement.
Compared to abrasive discs for weld cleaning, brushes are way more effective, cleaning only the welding debris and leaving the welding material base untouched; they are also less noisy and they generate less sparks so being a safer tool!
Advantages
01 - economical savings - minimum re-working costs, less setup
02 -user safety - less sparks and less or no (for encapsulated brushes) material/filament loss
Type of brushes
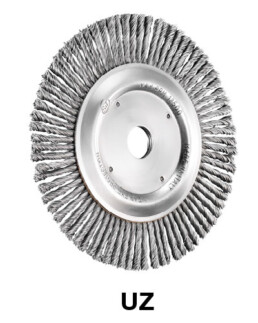
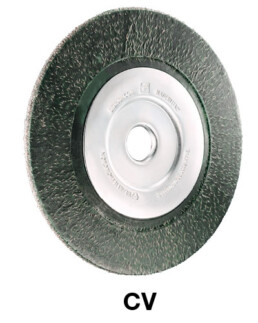
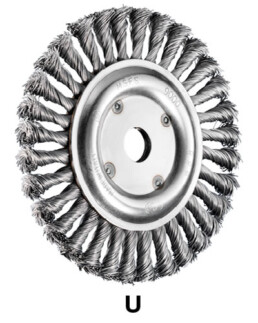
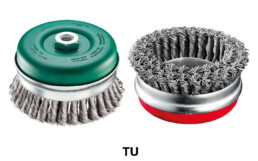
Wheel brushes UZ
UZ series brushes, with diameters from 115mm – 4-½” to 178mm – 7” are designed for the first welding layer brushing and they are also suitable for the removal of slugs inside every type of small slot. The chemical and mechanical characteristics of the steel (or stainless steel) wire, along with the outstanding engineered manufacturing process offer the users both high results for aggressiveness and durability.
Wheel brushes CV
CV series of encapsulated/vulcanised wheel brushes are made of a steel wire wheel ring bonded into a polyurethane solution. Main characteristics are:
regular trim wear out, constant and regular abrasive face width, no filament breakage → higher user safety.
Wheel brushes U
Twisted knots wheel brushes of the U series, with diameters from 100mm – 4” to 180mm – 7”, are especially suitable for the second welding layer and for the removal of tenacious slags.
Cups TU
Twist knot cup brushes, with diameter from 70mm – 3,75” to 150mm – 5,91”., with both 1 and 2 twist knot rows. They are suitable for the weld cleaning and thick slags removal over plain or lightly curved surfaces.
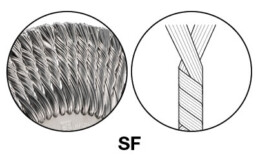
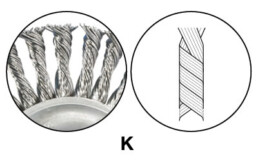
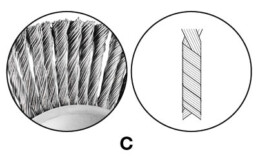
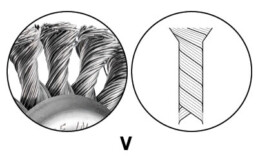
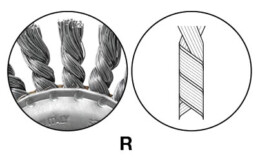
Pipe coating removal – CutBack
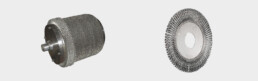
Polyethylene (PE), polypropylene (PP) or epoxy resin coating removal from the pipe ends is a critical operation and a performing brush strongly affects the productivity and the output quality.
Very high quality twist knot roller brushes in tempered steel made of several single section wheels provided both separately and assembled (ANU) are required for these processes.
The 3 operations of bevel cutting, cutback and edge cleaning are carried out in one step only by the same roller brush made of wheels of different diameter. Some of these brushes can be encapsulated for an increased performance.
Coated pipe cleaning roller brushes are supplied with special drilled cores in order to allow an eventual air cooling system in order to support very high temperatures and increase brush service life.
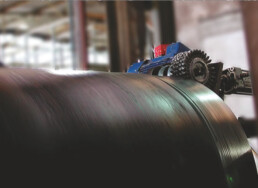
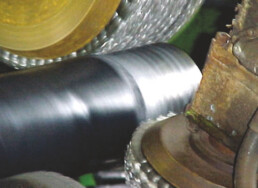
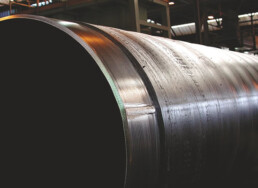
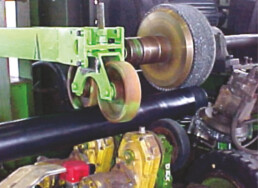
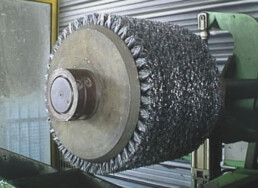
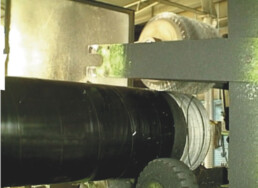

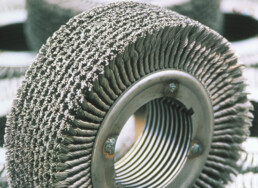
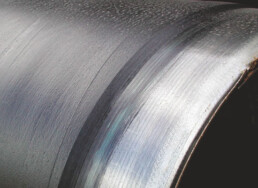
Pipe manufacturing prior to coating process
In the pipe manufacturing process many crimped steel wire brushes are used to maintain continuous electric contact between the welding nozzle and the moving steel pipe inside pipe welding units.
Thousands of filaments ensure continuous contact avoiding interruptions and imperfections of the weld seam.
Prior to coating process the pipe has to be transported through induction heating sections (ovens). Roller brushes made of single section twist knot wheels are recommended as an alternative to polyurethane (PU) rollers commonly used.
Indeed inside induction heating the pipes leaves the oven at a temperature higher than 150 °C – 302 °F. Poliurethane rollers at these temperatures get soft and damaged and wear out quickly requiring a frequent replacement (plant downtime).
Transport roller brushes (drive roll brushes) on the other side, with a perfectly trimmed surface and a very high fill density, don’t suffer these hard working conditions, they absorb vibrations of the welding seam rolling, they don’t damage the pipe and they have a service life many times higher than PU rollers. This way brushes ensure an economical saving and an immediate return on investment (less setups and lower plant downtime).
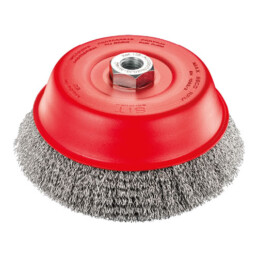
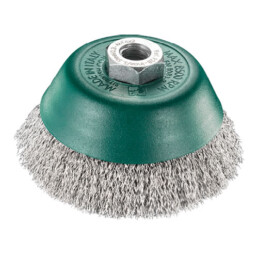
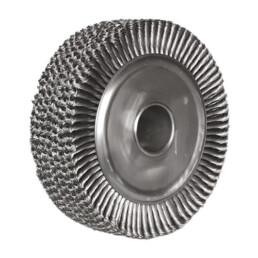
Post coating inspection: holiday detector
For customers requiring maximum reliability in detecting flaws, SIT proposes brushes able to adapt perfectly to each pipe’s surface allowing the available testing equipment to discover the minimal imperfection.
These strip brushes have soft and long stainless steel wire which ensures electric contact without damaging the coating and adapting to different pipe diameters.
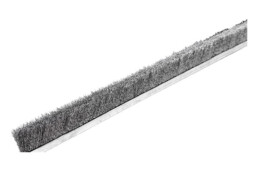
Concrete coating, weight coat/compression coat/shotcrete on pipes
Concrete weight coating is the operation of projecting at high speed a layer of concrete with fiber reinforcement over the external surface of the pipe. It’s widely used and recommended for underwater/subsea pipelines in order to avoid flotation since buoyancy force is higher than the pipe weight.
Shotcrete can be applied over any anti-corrosion and insulation coating systems giving “weight” (negative buoyancy) and giving also a special passive corrosion protection.
Concrete is sprayed on the pipe’s surface with a special machine (side wrap application) mounting a technical roller brush made of very high resistance crimped wire single section wheels (INCO).
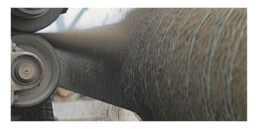
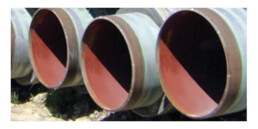
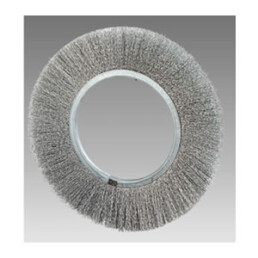
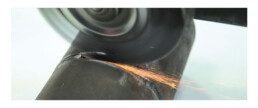
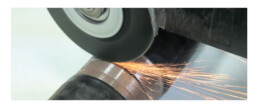
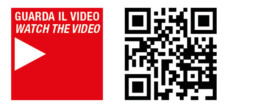