INDUSTRIAL APPLICATIONS
Brushes for rolling mills
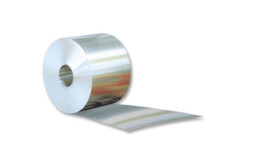
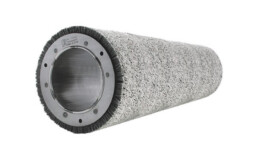
Manufacturing types
Technical Brushes for rolling mills and pickling can be mounted on a tube or on a shaft with hubs. Cores can be single-use or reusable.
Brushes for pickling and generally single section wheels and spiral brushes are mounted on the core with hubs and locking flanges that allow a fast replacement of the brush. Every item is designed and built in accordance to customer’s needs (mounting and processing).
SIT Tecnospazzole offers to its customers the service of returning the brush worn out to reuse the core. This way the customer has an economical saving and a lower environmental impact.
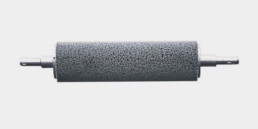
Materials, types of surface and filaments
Treated surface can be ferrous (carbon steel and stainless steel) or non-ferrous (aluminium and special alloys). Depending on the type of required finishing, filament with rectangular or oval or circular section can be used.
In primary metal industry speed issues and mechanical limitations of existing lines make the filament of the roller brushes the only variable to work on in order to increase cleaning performance. SIT’s customers can choose among a wide range of synthetic filaments (monofilament and even multi filament) or metallic wires.
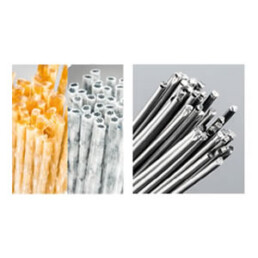
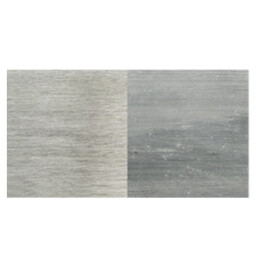
ALUMINIUM
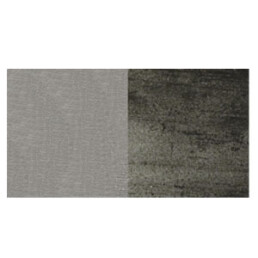
STEEL
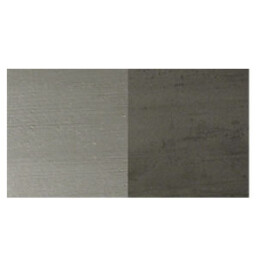
INOX
Filaments used for laminating brushes
Applicazione | Application | Filamento | Filament |
---|---|---|---|
Lavaggio | Washing | Nylon 6.6 / PPL | Nylon 6.6 / PPL |
Lucidatura | Polishing | Nylon Abrasivo Grana 2000-600 Ossido di Alluminio | Abrasive Nylon Grit 2000-600 Aluminium Oxide |
Finitura | Finishing | Nylon Abrasivo Grana 500-240 Ossido di Alluminio | Abrasive Nylon Grit 500-240 Aluminium Oxide |
Asportazione | Removal | Nylon Abrasivo Grana 180-80 Carburo di Silicio | Abrasive Nylon Grit 180-80 Silicon Carbide |
Forte Asportazione (Rottura scaglia superficiale) | Strong Removal (Breaking the surface chippings) | Nylon Abrasivo Grana 60-36 Carburo di Silicio | Abrasive Nylon Grit 60-36 Silicon Carbide |
Distinguishing characteristics of SIT Brushes
- Perfect cylindricity
- Perfect surface trimming
- Very high fill density
- Very high quality of support materials and filaments
- Precise dynamic balancing followed by a certificate
- Cost optimization for customers thanks to regeneration of brush shafts
Minimum and maximum size achievable
SIT can manufacture a wide range of brushes for dimensions and type. In order to satisfy customer needs, brushes’ cores and adapters are manufactured on drawing according to specific requirements of the rolling mill plant on which they will be mounted.
MIN -> MAX | ||
---|---|---|
mm | in | |
Diametro esterno / Outer diameter | 150 -> 600 | 5-7/8 -> 23-5/8 |
Lunghezza / Length | 400 -> 6000 | 15-3/4 -> 236-1/4 |
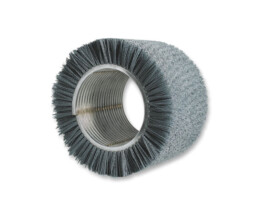
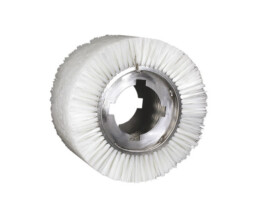
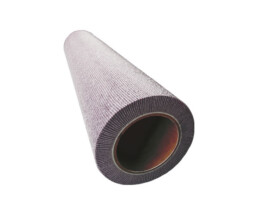
Roller brushes for primary metal industry applications
- Cleaning, Galvanizing Linea (CGL, HDGL) → Cleaning, removal of impurities and milling oil in alkali brushing and water brushing
- Hot Pickling Line (HPL) → Pre and post pickling water brushing
- Annealing Line (CAL) → Cleaning, degreasing, polishing
- Cold Stainless Annealing and Pickling Lines (CAPL) → Water brushing and polishing after acid pickling
- Electrogalvanizing Line (EGL)
- Bright Annealing Line (BAL)
- Sheet/Panel washing machines → Blank washer oil brushing before stamping (automotive) and aluminum alkali brushing (aircraft)
Equipment range
- Brushing units in cleaning and electrolytic degreasing sections
- Brushing units after scale breaker units
- Brushing units after pickling tanks
- Brushing units in quench section
- Brushing units in finishing lines (slitter, cut-to-length, blanking…)
- Polishing rolls units in CRM
Brush function
- Alkaline brushing
- Hot water brushing
- Cold water brushing
- Surface cleaning
- Roll polishing
- Surface finishing
- Descaling/pickling
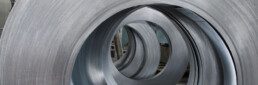
Recommended operating parameters
- Filament pH range service: 3-14
- Brush roll recommended speed: 750-900 RPM
- Brush roll max. service speed: 1000 RPM
- Brush roll range service temperature: 65 -> 85 °C – 149 -> 185 °F
- Brush roll bristles depth of penetration: 1->5mm – 0.04”->0.2”
Trimming and balancing
Rolling mills brushes have a special trimming (or even grinding in case of metallic wire) and a dinamyc balancing according to ISO 1940 (ISO 1940 g. 6,3 as standard)
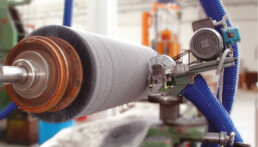
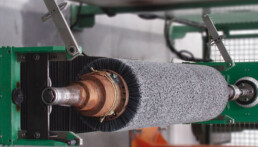